Warehouses are extremely important for every industry that produces or sells products, making it a huge industry on its own. However, places with a lot of workers who perform labor around heavy machinery are dangerous. Injuries aren’t uncommon inside a warehouse, especially if people ignore the proper steps and necessary care. Avoiding the resulting injuries is why it’s so important that every warehouse manager learn the best practices for mitigating warehouse liabilities.
Risk Assessment
The first thing many businesses can do to improve their employees’ safety is a risk assessment. This is like an inspection where someone comes in and examines your company’s practices and processes to ensure there are no working hazards. This is very important, as the outside view can reveal a lot of inefficiencies and dangerous situations you might miss in an internal review.
Fire
Warehouses can store a lot of dangerous and flammable materials while using heavy equipment for transportation and storage. This can spell disaster if the proper precautions aren’t in place, as the materials could go up in flames. Invest in fire suppression equipment and train employees to recognize dangerous situations and how to respond properly.
Floods
Although floods aren’t as inherently dangerous as fires, they can still cause a lot of damage to equipment and inventory and endanger the lives and well-being of employees. Keep any inventory that’s susceptible to water damage off the ground and properly maintain your pipes for the best chance of mitigating floods.
Security
Another step that helps with mitigating warehouse liabilities is increasing the security in the workspace. Invest in security that limits and tracks entry into your warehouse, so you can reduce thefts. You can also get security cameras, which help reduce cases of improper behavior from everyone in your warehouse.
Preventative Maintenance
It’s always best to find and fix a hazard before it fully breaks down and hurts someone. By that point, it’s already much too late and will cost you a lot more money and potentially cause your workers injury. Preventative maintenance starts by following the maintenance schedule that comes with most equipment and should include frequent inspections of your facilities as well.
Inspections
A huge part of preventative maintenance is discovering problems before they happen, which is why frequent inspections are a necessity for good safety in your warehouse. For the best results, you should hire a company that specializes in warehouse rack inspections. These inspections should happen every week, if not more frequently, to catch as many hazards as possible. You don’t need to run full inspections on everything but look at the parts of your warehouse that contain the most potential for hazards and the parts of equipment most prone to wear. This will help you quickly identify problems and fix the issues before workers get hurt or something damages your product.
Policies
Outside of inspections and preventative maintenance, policy changes are extremely important for the safety of everyone in your warehouse. This section will talk in detail about what your policies should be aiming for and how they can best support your workers’ safety. Only by implementing proper policies can you truly help protect your workers.
Employee Equipment
There are a lot of things that can break, which can hurt employees, but many injuries happen because of simple accidents and human error. A great way you can reduce accidents is with equipment that focuses on safety as well as efficiency. Most equipment comes with some safety features, but only investing in equipment that promotes worker safety is a smart plan.
Work Culture
Another focus of your policy-making should be improving your work culture, so it focuses on employee safety. A lot of workplace injuries happen because people feel they need results as soon as possible, even if getting them forgoes safety. Fostering a work culture that encourages workers to value their own safety is the best way to avoid these accidents and can massively increase the quality of work, as people aren’t rushing as much.
Safe Task Assignments
One policy every warehouse and workplace should enforce is that only the right people should do the right jobs. This means only those with the proper training should operate heavy machinery or handle hazardous materials. This will prevent a lot of accidents in the future, even if it does slow down production a bit.
Proper Organization
People often underestimate how useful a proper organization plan can be for efficiency and safety. Take the time to create a good layout that everyone can easily follow, as this will help your workers navigate your warehouse safely and efficiently. This can be especially useful for heavy machinery, as good signs and organization can lower the chances of accidents with heavy machinery.
Training
One of the biggest changes you can make for your workforce’s safety is including mandatory and optional safety training. At the very basic level, this training will help your employees understand how to deal with emergency situations and learn more about the best practices for safety in the workplace. However, there are many other benefits that come from hosting frequent training sessions that boost safety and efficiency across the business.
Better Workforce
One of the main benefits of training, outside of learning safety procedures, is that workers will learn the best practices for their jobs as well. Training will teach them the newest ideas on working efficiently without putting themselves at risk. These training sessions are an investment that makes your workers better at their jobs.
Communication
A large part of inefficiency and accidents at work happen because of a misunderstanding or miscommunication. However, training helps clear up these misunderstandings without risking the lives of employees. Since everyone is learning the same policies and procedures, there should be a lot less confusion among employees.
These are the best practices you can enforce for the safety of your employees in the warehouse. By implementing these strategies at your business, you can vastly improve the work quality of your employees, increasing morale and safety across the board. Although it may seem like a high cost to include things like training or new equipment, it’s an investment in your workers and will quickly pay for itself if done correctly.
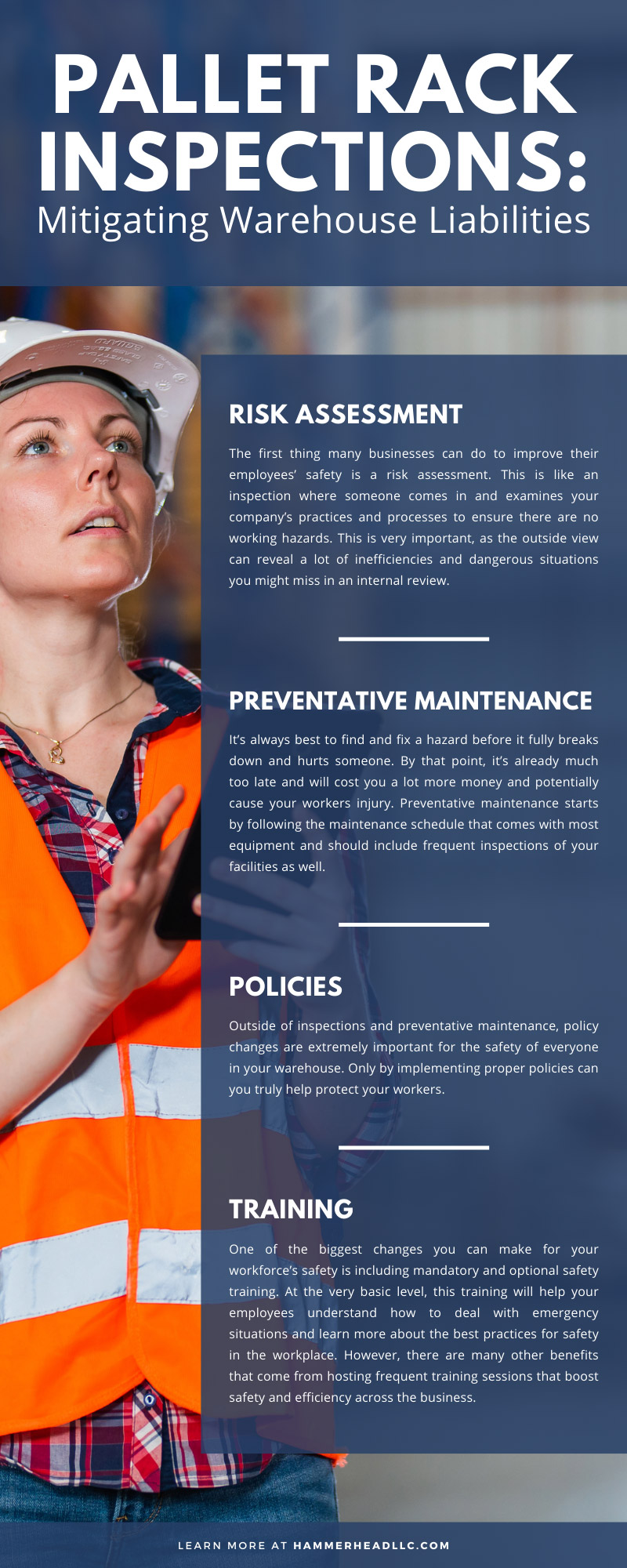